The Repair Lab: where alternative repair solutions get to see the light of day
'An innovative breeding ground'. Not the first thing you think of when you enter the somewhat dated KLM building 425 at Schiphol-East. Orange ball lights on the ceiling of the canteen. A stairwell so characteristic that it seems as if time has stood still here since 1972... Nothing could be further from the truth; this is where the Engineering & Maintenance Repair Lab innovates, in 2022 style!
The Repair Lab: where alternative repair solutions get to see the light of day
'An innovative breeding ground'. Not the first thing you think of when you enter the somewhat dated KLM building 425 at Schiphol-East. Orange ball lights on the ceiling of the canteen. A stairwell so characteristic that it seems as if time has stood still here since 1972... Nothing could be further from the truth; this is where the Engineering & Maintenance Repair Lab innovates, in 2022 style!
The eye-catcher in the middle of the Repair Lab is a conference table made from an aircraft engine. A little further and you find a table, which was a wing in a previous life, full of 3D printed objects. Creativity at its best. The Repair Lab space exudes the versatility of the team that Jeroen van Vliet has been leading for two years.
The team is small and young. They draw, certify and design. 'We aim to develop and implement alternative repairs for the cabin and aircraft components in a structured manner. This enables us to reduce costs for KLM, increase component reliability and shorten delivery times', Jeroen says. 'There is also an eye for design which sometimes results in beautiful products or prototypes.'
The eye-catcher in the middle of the Repair Lab is a conference table made from an aircraft engine. A little further and you find a table, which was a wing in a previous life, full of 3D printed objects. Creativity at its best. The Repair Lab space exudes the versatility of the team that Jeroen van Vliet has been leading for two years.
The team is small and young. They draw, certify and design. 'We aim to develop and implement alternative repairs for the cabin and aircraft components in a structured manner. This enables us to reduce costs for KLM, increase component reliability and shorten delivery times', Jeroen says. 'There is also an eye for design which sometimes results in beautiful products or prototypes.'
Cheaper and more attractive
The soap bottle holder in the shape of a lush orange tulip didn’t make the cut, but its successor – a sleek white soap bottle holder – did, and is installed on board the current Boeing 737-800 fleet. Jeroen: 'The new 3D-printed design is, a lot more attractive for the passengers and a lot cheaper for KLM. For the B737 and the B777, this modification saves over €60,000 annually in man hours and material costs! In addition, in-house design and implementation also reduces costs even further. The new design was created together with other KLM departments, such as Customer Experience and Cabin Engineering'.
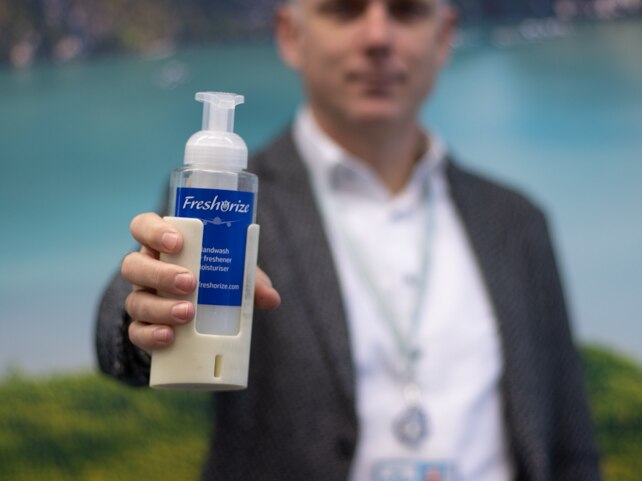
Flying carpet
The Repair Lab's assessment is based on key questions: what are the normal repair costs, are there any delivery problems, is it feasible and are we bound to any contracts? Sometimes it's a question of killing several birds with one stone. For example, the case where Jeroen and his team developed a new way of cutting and laying carpet in the Boeing 787-9. The original carpet layout of the Boeing 737-800 and Boeing 787-9 had a disadvantage. Jeroen explains. 'If you needed to replace carpet under the seats, the seats had to be taken out to remove the entire piece of four meter long carpet. An intensive process, requiring several technicians.'
Flying carpet
The Repair Lab's assessment is based on key questions: what are the normal repair costs, are there any delivery problems, is it feasible and are we bound to any contracts? Sometimes it's a question of killing several birds with one stone. For example, the case where Jeroen and his team developed a new way of cutting and laying carpet in the Boeing 787-9. The original carpet layout of the Boeing 737-800 and Boeing 787-9 had a disadvantage. Jeroen explains. 'If you needed to replace carpet under the seats, the seats had to be taken out to remove the entire piece of four meter long carpet. An intensive process, requiring several technicians.'
Quick change thanks to Velcro
'The most important elements of the new method are: we cut the carpet, we lay it in much smaller pieces and the carpets are no longer stuck to the aircraft with tape. This means that the floor no longer needs to be cleaned for carpet installation. We now install the carpet with a type of Velcro, which doesn’t need to be replaced during carpet changes. In addition, a piece of carpet can easily and quickly be replaced if it really can’t be cleaned. A great project in which we worked closely with other departments within Engineering & Maintenance.'
Quick change thanks to Velcro
'The most important elements of the new method are: we cut the carpet, we lay it in much smaller pieces and the carpets are no longer stuck to the aircraft with tape. This means that the floor no longer needs to be cleaned for carpet installation. We now install the carpet with a type of Velcro, which doesn’t need to be replaced during carpet changes. In addition, a piece of carpet can easily and quickly be replaced if it really can’t be cleaned. A great project in which we worked closely with other departments within Engineering & Maintenance.'
Resplendent repairs
Another example of a part which KLM repairs instead of throwing away, thanks to the Repair Lab, is the axle of an air cycle machine on board. Jeroen: 'This is part of the cabin air conditioning system in the B787. The shaft wears out during use and over time, the chrome becomes scratched. A mechanic would normally have to replace it with a new one. Our team came up with a solution. What happens if we remove the chrome layer from the axle and apply a new layer? This turned out to be a great solution! This method has of course been tested and approved, and we are carrying it out in close cooperation with Engineering, Component Services and EPCOR. The old component now lasts as long as a new shaft, and is more sustainable, because we don't have to throw anything away!'
Resplendent repairs
Another example of a part which KLM repairs instead of throwing away, thanks to the Repair Lab, is the axle of an air cycle machine on board. Jeroen: 'This is part of the cabin air conditioning system in the B787. The shaft wears out during use and over time, the chrome becomes scratched. A mechanic would normally have to replace it with a new one. Our team came up with a solution. What happens if we remove the chrome layer from the axle and apply a new layer? This turned out to be a great solution! This method has of course been tested and approved, and we are carrying it out in close cooperation with Engineering, Component Services and EPCOR. The old component now lasts as long as a new shaft, and is more sustainable, because we don't have to throw anything away!'
Data is key
Data helps Jeroen and his team even more than ever to predict alternative repairs. 'Sometimes you tend to make a choice based on your gut feeling but data gives us more insight and facts about the parts we spend the most money on and which choices we need to make. The mechanics in the shops are also good advisors; they literally see every broken part pass through their hands and are a good indicator of what can be done differently or better. Needless to say, we are often present on the shop floor to see where we can improve'.
Data is key
Data helps Jeroen and his team even more than ever to predict alternative repairs. 'Sometimes you tend to make a choice based on your gut feeling but data gives us more insight and facts about the parts we spend the most money on and which choices we need to make. The mechanics in the shops are also good advisors; they literally see every broken part pass through their hands and are a good indicator of what can be done differently or better. Needless to say, we are often present on the shop floor to see where we can improve'.
Making sustainability tangible
The continuous search for improvement and cost efficiency gives Jeroen and his team a lot of energy: 'The work itself is always fun. The subjects and departments that we deal with both inside and outside KLM are extremely diverse. We have freedom and are given a lot of responsibility. We work with motivated people. Last but not least: we work on tangible projects that ultimately save money and lead to sustainability or product improvement. When I look outside and see an aircraft take off, it fills me with pride.'
Making sustainability tangible
The continuous search for improvement and cost efficiency gives Jeroen and his team a lot of energy: 'The work itself is always fun. The subjects and departments that we deal with both inside and outside KLM are extremely diverse. We have freedom and are given a lot of responsibility. We work with motivated people. Last but not least: we work on tangible projects that ultimately save money and lead to sustainability or product improvement. When I look outside and see an aircraft take off, it fills me with pride.'